Plastotecnica SpA, azienda italiana all’avanguardia, produce film plastici di alta qualità per diverse applicazioni, tra cui il settore alimentare e industriale. Forte di una lunga esperienza e orientata all’innovazione, si distingue per l’eccellenza dei prodotti e l’attenzione al cliente.
Con l’esigenza di prepararsi alla certificazione BRCGS, e di conseguenza dover riorganizzare la propria logistica, Plastotecnica ha deciso di coinvolgere Kaizen Key.
Questo caso studio illustra le sfide affrontate, le soluzioni adottate ed i miglioramenti ottenuti grazie all’implementazione di un approccio di miglioramento dei processi strutturato.
Focus sulle esigenze specifiche di Plastotecnica
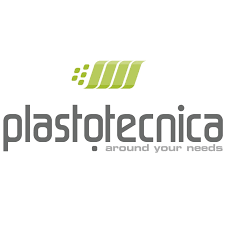
- Requisito di certificazione BRCGS: Plastotecnica stava attivamente perseguendo la certificazione BRC Global Standards, un requisito fondamentale per molti dei suoi clienti, in particolare nel settore degli imballaggi alimentari;
- Separazione logistica obbligatoria: un requisito chiave di BRCGS è la chiara separazione delle operazioni logistiche interne ed esterne. Ciò rappresentava una sfida significativa per il layout e i processi esistenti di Plastotecnica;
- Preoccupazioni per il carico di lavoro: la principale preoccupazione di Plastotecnica era che questa suddivisione dei compiti avrebbe aumentato il carico di lavoro per il proprio personale logistico, potenzialmente riducendo l’efficienza complessiva anziché migliorarla. Erano preoccupati per:
- L’aggiunta di passaggi di movimentazione extra;
- La creazione di distanze di percorrenza più lunghe;
- La necessità di più personale;
- Inefficienze esistenti: oltre a BRCGS, Plastotecnica aveva già identificato possibili spunti di miglioramento nella sua logistica interna:
- Aree di stoccaggio dislocate in aree non ottimali del plant produttivo;
- Bassi livelli di servizio e scarsa utilizzazione degli operatori;
- Percorsi di carrelli elevatori nelle aree produttive;
- Dati imprecisi sulla movimentazione dei materiali;
- Elevati livelli di stock (capitale immobilizzato).
Approccio di Kaizen Key
Kaizen Key ha implementato un approccio strutturato incentrato su:
- Analisi: mappatura dettagliata dei flussi di materiali, dei movimenti dei pallet e della saturazione degli operatori in tutti i reparti;
- Lavoro con un team interfunzionale, che coinvolgesse membri di diversi reparti;
- Principi Lean: applicazione delle metodologie Lean per identificare ed eliminare i Muda;
- Miglioramento dei processi: focus sul miglioramento dei flussi dei processi, della movimentazione dei materiali e dell’utilizzo dello spazio;
- Formazione e responsabilizzazione: Kaizen Key ha fornito formazione al personale, promuovendo un senso di responsabilità e coinvolgimento nel processo di miglioramento continuo;
- Miglioramento a piccoli passi: implementazione delle soluzioni passo dopo passo con un impatto concreto, immediato e positivo;
- Decisioni basate sui dati: utilizzo dei dati per comprendere lo stato attuale, definire gli obiettivi di miglioramento e misurare l’impatto dei cambiamenti.
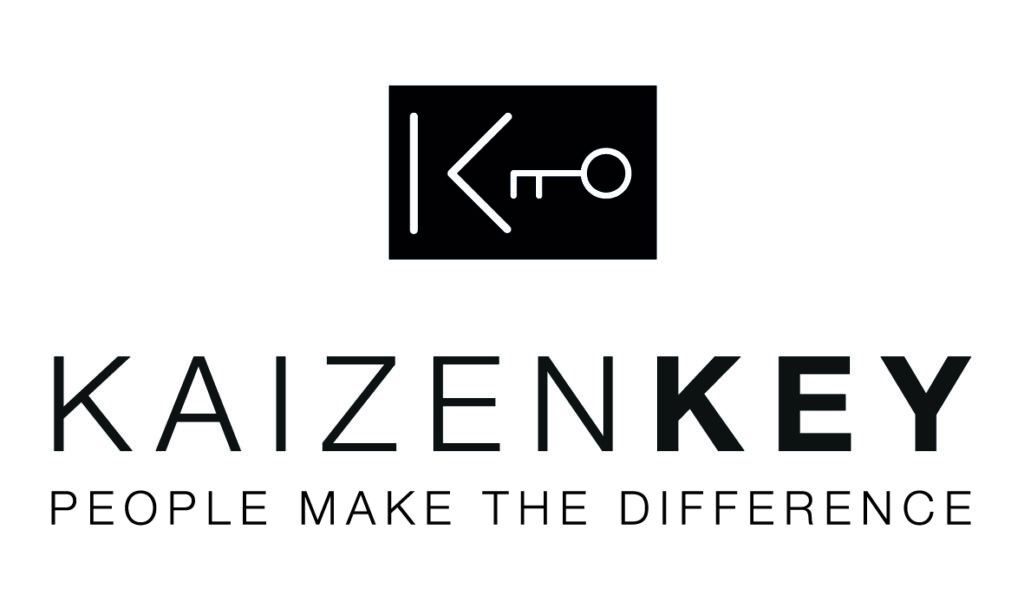
Azioni chiave e soluzioni
- Creazione di “Aree Grigie”: implementazione di “aree grigie” designate per creare zone tampone per il flusso dei materiali, migliorare l’organizzazione e supportare la certificazione BRCGS. Queste aree sono state progettate per ospitare i materiali in entrata nei reparti e i prodotti in uscita, semplificando il flusso e migliorando la sicurezza;
- Sono state identificate due possibili opzioni di riorganizzazione, ed entrambe le soluzioni sono state valutate in base a diversi fattori, quali le percorrenze della logistica e gli investimenti necessari per arrivare alla configurazione finale;
- Formazione del team logistico: è stato creato e formato un nuovo team logistico dedicato;
- Procedure standardizzate: redazione di Procedure Operative Standard (SOP) sulla base delle quali sono stati formati gli operatori;
- Layout migliorato: riorganizzazione del layout, compresa l’area di imballaggio e di alcune zone di stoccaggio materiali;
- Digitalizzazione: implementazione di un’applicazione per la gestione delle operazioni logistiche secondo i nuovi standard definiti.
Risultati
I cambiamenti implementati hanno portato a miglioramenti significativi:
- Maggiore efficienza, legata alla riduzione delle distanze di percorrenza: le percorrenze in alcuni reparti sono state ridotte addirittura del 58%;
- Bilanciamento del carico di lavoro degli operatori;
- Maggiore sicurezza: ridotti i rischi eliminando i carrelli elevatori dalle aree di produzione e implementando una migliore gestione del traffico;
- Conformità BRCGS: l’azienda ha ottenuto valutazione favorevole, di grado A, durante l’audit di certificazione ed è in attesa del rilascio del certificato BRC con la creazione di aree grigie conformi e gestione separata dei carrelli;
- Riduzione degli sprechi: ottimizzati i flussi di materiali e ridotta la necessità di rilavorazioni;
- Migliore gestione delle scorte di magazzino: l’azienda ha migliorato la gestione dello stock attraverso sistemi e processi migliorati;
- Migliore utilizzo dello spazio: migliorato l’utilizzo dello spazio attraverso un migliore Layout e soluzioni di stoccaggio;
- Ridotto il numero di carrelli elevatori in uso all’interno delle aree produttive del 50%;
- Ridotto del 10% il numero di risorse dedicate a parità di servizio alla produzione;
- Certezza dei tempi di risposta da parte della logistica;
- Creazione dei presupposti per sviluppare progetti di progressiva automazione per le attività ripetitive quali l’imballaggio pallet e trasferimento a magazzino.
Conclusione
La partnership tra Plastotecnica e Kaizen Key dimostra la potenza di un approccio strutturato e basato sui dati per il miglioramento della logistica. Applicando i principi Lean, concentrandosi sul lavoro di squadra e implementando soluzioni pratiche, Plastotecnica è stata in grado di ottenere significativi miglioramenti operativi, migliorare la sicurezza e avvicinarsi all’ottenimento della certificazione BRCGS.
Contattaci per scoprire come possiamo aiutare la tua azienda!