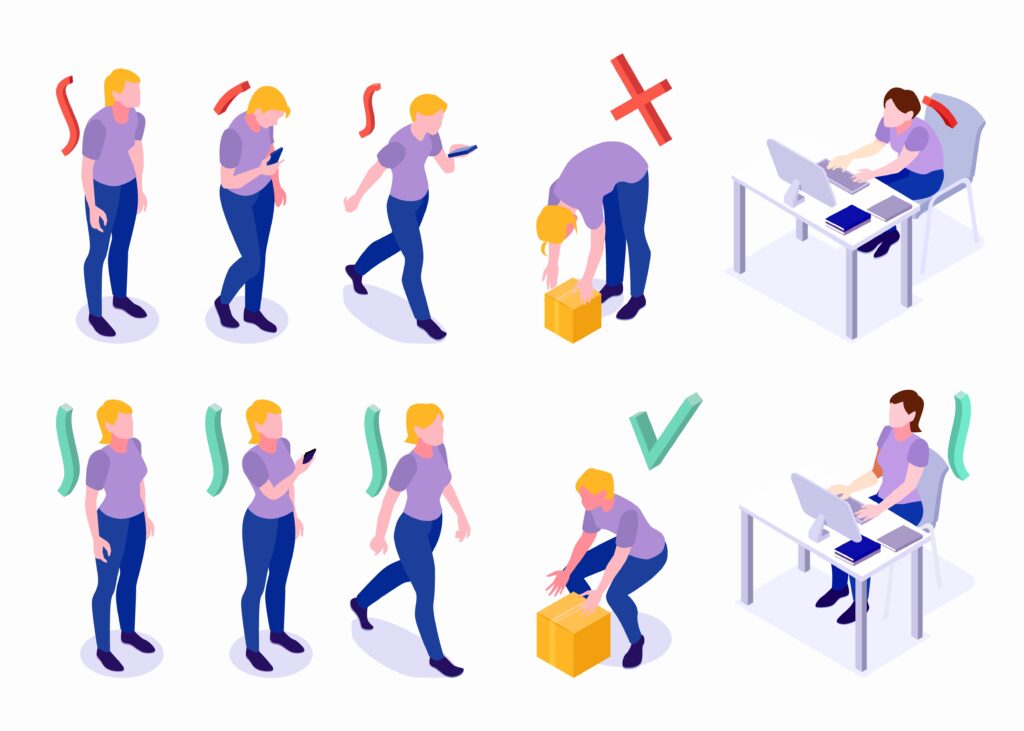
Valutazione delle posture di lavoro: il metodo di OWAS
Negli ambienti industriali, la salute e la sicurezza degli operatori sono di primaria importanza. Un aspetto cruciale da considerare è la postura di lavoro, poiché una postura scorretta può portare a danni muscolo-scheletrici nel tempo. In questo contesto, il Metodo OWAS (Ovako Working Posture Analysing System) si presenta come uno strumento efficace sviluppato originariamente nell’industria metallurgica finlandese negli anni ’70.
OWAS: il contesto storico
Il sistema di analisi delle posture di lavoro noto come OWAS (Ovako Working Posture Analysing System) è stato sviluppato negli anni ’70 dal Finnish Institute of Occupational Health in collaborazione con l’Association of Finnish Steel and Metal Producers. Originariamente concepito per l’industria metallurgica finlandese, il metodo OWAS mira a riconoscere le posture che potrebbero comportare rischi per la salute e valutare il livello di rischio in base agli effetti combinati di diverse posture e carichi di forza.
La procedura pratica coinvolge l’osservazione dei lavoratori a intervalli regolari, solitamente ogni 30-60 secondi. Durante questo periodo rappresentativo, vengono registrate le posture assunte e gli sforzi esercitati. I dati raccolti vengono successivamente normalizzati e analizzati per valutare i livelli di rischio. Il risultato di questa analisi è la determinazione delle “categorie di azione”, che indicano gli interventi consigliati in base al livello di rischio derivante dalla combinazione specifica di posture. Queste categorie vanno dalla situazione in cui non è richiesto alcun intervento a casi che richiedono una correzione immediata.
Monitoraggio e valutazione delle posture
Il Metodo OWAS si focalizza sul monitoraggio delle posture di lavoro, concentrandosi in particolare sulla schiena, braccia, gambe e il carico sollevato dagli operatori. Questo approccio prevede un processo di valutazione suddiviso in tre fasi chiave:
OWAS fase 1: codice della postura
Ogni postura viene rappresentata da un codice a quattro cifre (XYZW), dove ogni cifra indica il livello di rischio per la schiena, le braccia, le gambe e il carico sollevato. Questo passo consente una dettagliata categorizzazione delle posture adottate durante le attività lavorative.
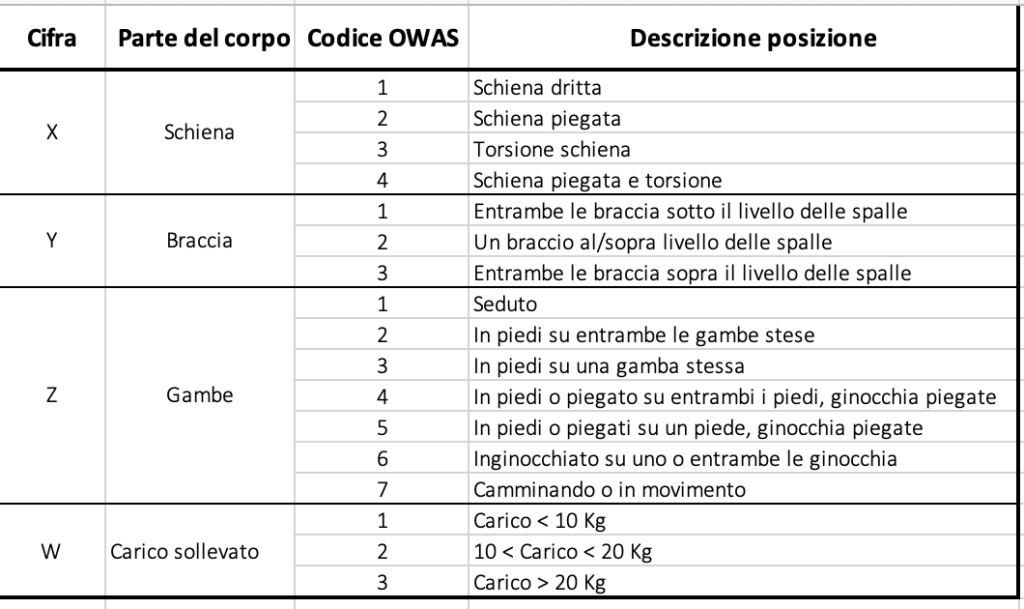
OWAS fase 2: categoria di rischio
Utilizzando il codice della postura, si determina la categoria di rischio attraverso un confronto con una tabella specifica. La categoria di rischio, espressa da un numero da 1 a 4, indica se una postura richiede misure correttive per prevenire danni muscolo-scheletrici. Le misure correttive variano a seconda della categoria di rischio.
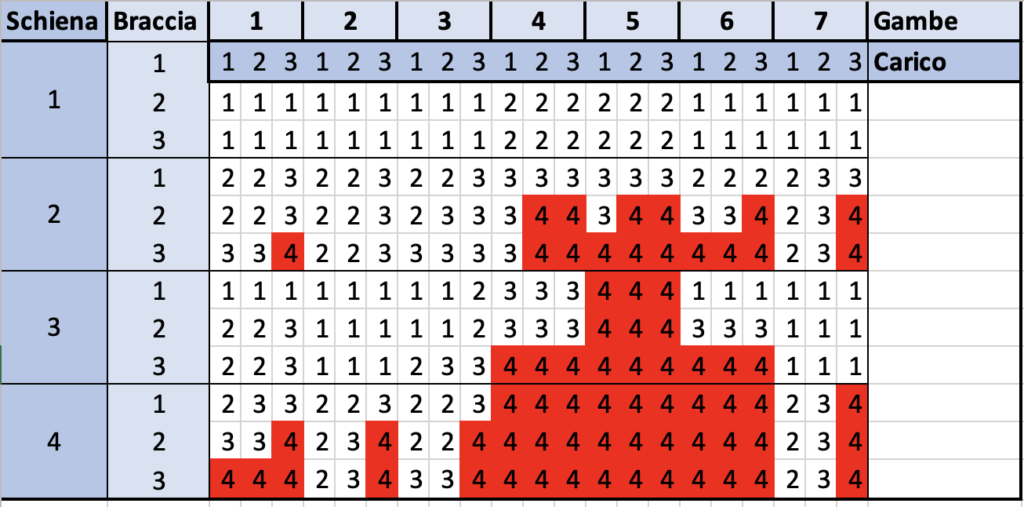
OWAS fase 3: calcolo dell’indice di OWAS
L’indice OWAS si calcola considerando le frequenze percentuali di osservazioni nelle diverse classi di rischio. Questo indice riflette il livello complessivo di rischio associato alle posture assunte dagli operatori nel corso del tempo.
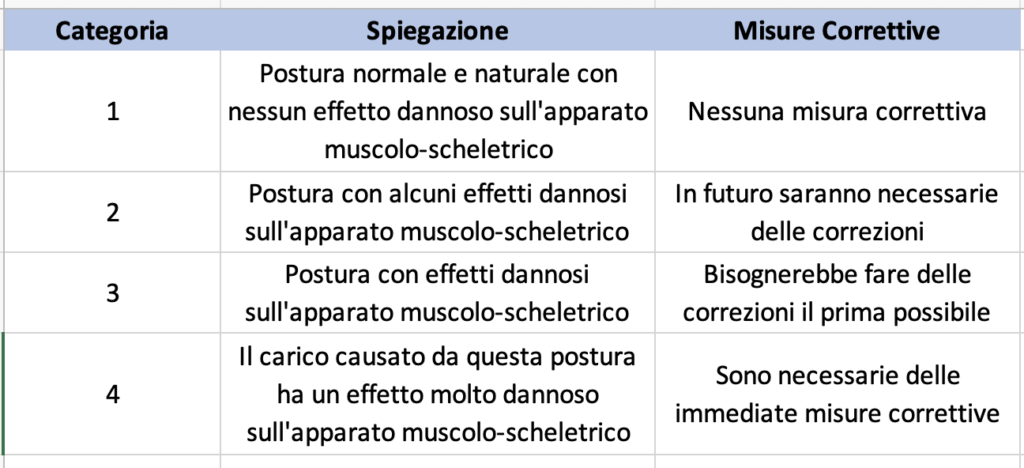
OWAS fase 4: calcolo livello di rischio
Si individuano quattro diversi livelli di rischio in base al valore assunto dall’indice questi livelli descrivono l’attività in esame e indicano quanto può essere
dannosa per la salute dell’operatore.
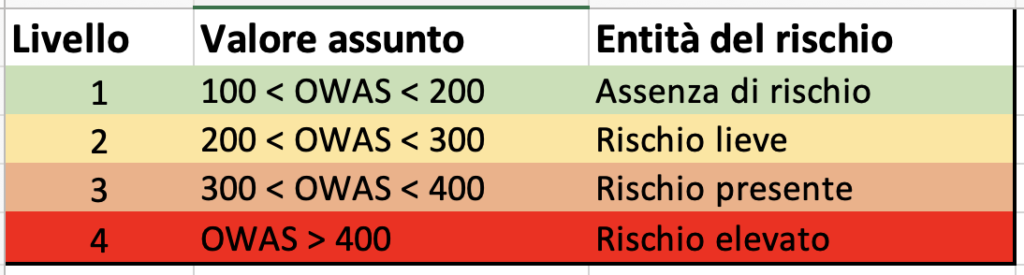
Questo sistema permette di individuare in modo sistematico quali attività richiedono una modifica e anche in che misura deve essere eseguita questa modifica, un’attività con un livello di rischio pari a 4 necessita di un intervento immediato e deve precedere le attività con livello di rischio 3 e 2. Così facendo è possibile organizzare in modo più efficiente il sistema di correzione dei problemi legati alle attività svolte dagli operatori e ottimizzare al meglio le risorse dell’azienda, evitando sprechi in termini di tempo e denaro.
OWAS: Implementazione e benefici
L’implementazione del Metodo OWAS offre diversi vantaggi nell’ambito dell’industria Lean Manufacturing, dove l’efficienza e la sicurezza sono prioritarie.
OWAS: l’identificazione sistematica dei problemi
Il sistema di OWAS permette un’identificazione sistematica delle attività che richiedono modifiche, consentendo alle aziende di concentrare le risorse sulle aree ad alto rischio. Le attività con un livello di rischio più elevato ricevono attenzione prioritaria.
L’approccio consente un’ottimizzazione delle risorse aziendali, evitando sprechi di tempo e denaro. Le attività a rischio elevato vengono affrontate tempestivamente, migliorando la salute degli operatori e riducendo il potenziale impatto negativo sulla produzione.
Miglioramento continuo dei processi
Il Metodo OWAS fornisce una base solida per un miglioramento continuo dei processi, poiché consente un’analisi dettagliata delle posture di lavoro nel tempo. Le modifiche apportate in risposta ai risultati dell’analisi contribuiscono a creare un ambiente di lavoro più sicuro e efficiente.
In conclusione, l’implementazione del Metodo OWAS nell’industria della Lean Manufacturing si rivela un passo significativo verso la creazione di ambienti di lavoro più sicuri, migliorando contemporaneamente l’efficienza operativa. La combinazione di monitoraggio sistematico e interventi mirati contribuisce a preservare la salute degli operatori e a ottimizzare le risorse aziendali.
Leggi tutto sull’ergonomia sui nostri articoli:
1. Ergonomia: il metodo di NIOSH
2. Ergonomia: guida pratica per prevenire i rischi!